Milling Feed Rate Calculator | Metric/Imperial, Chip Load & Materials
Milling is a crucial machining process used to cut, shape, or remove material from a workpiece. One of the most critical parameters in milling is the feed rate. Calculating the correct feed rate is essential for ensuring efficiency, accuracy, and extending the lifespan of cutting tools.
Today, we will thoroughly explore the concept of feed rate, provide formulas, examples for both metric and imperial units, and introduce our Milling Feed Rate Calculator to streamline your work. This guide will help you learn how to calculate milling feed rate, optimize your machining parameters and make the most out of your milling operations.
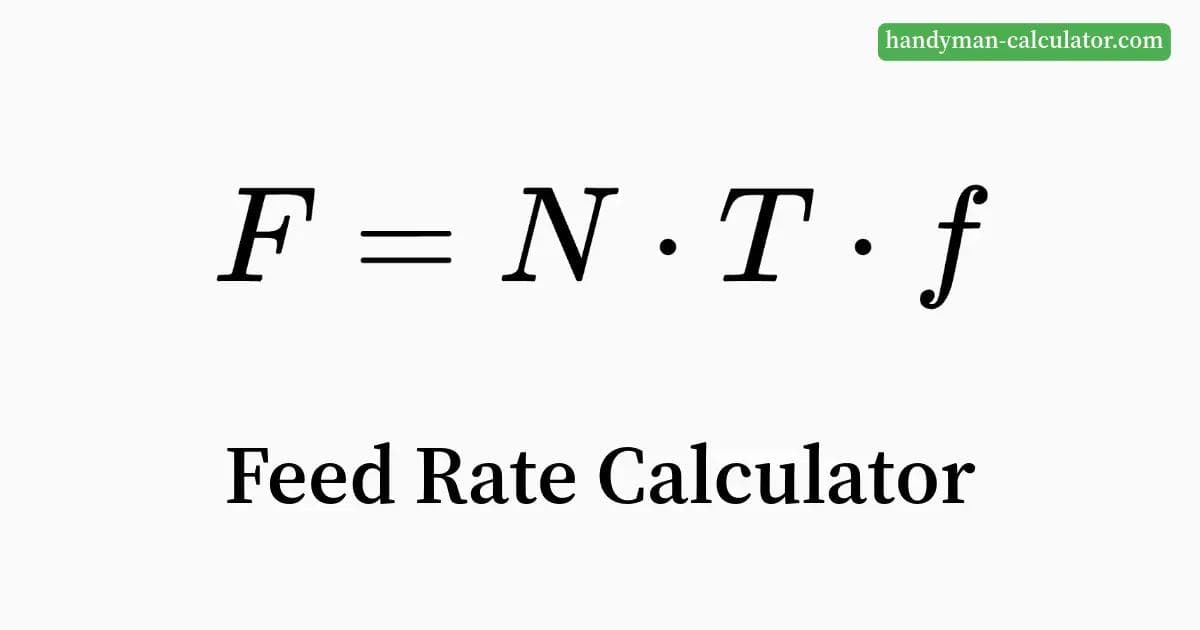
What is Feed Rate in Milling?
Feed rate refers to the distance the cutting tool or the workpiece moves relative to each other in one minute. It is typically measured in millimeters per minute (mm/min) in the metric system or inches per minute (IPM) in the imperial system. The feed rate significantly affects:
- Machining speed: How quickly material is removed. Higher feed rates mean faster material removal, but going too fast can have negative consequences.
- Tool life: Excessive feed rates can lead to accelerated tool wear and breakage.
- Surface finish: Inappropriate feed rates can result in poor surface finishes or reduced accuracy. Optimizing the feed rate is crucial for achieving the desired surface quality.
The Milling Feed Rate Formula & Chip Load
The fundamental formula for calculating feed rate is:
Where:
- =Feed rate (mm/min or IPM).
- =Spindle speed (revolutions per minute or RPM).
- =Number of teeth on the cutting tool.
- =Feed per tooth (mm/tooth or inch/tooth). This is sometimes also referred to as chip load.
What is Chip Load?
Chip load, represented by 'f' in the formula, refers to the amount of material removed by each tooth of the cutting tool per revolution. It's a critical parameter that dictates the thickness of each chip being cut. Too high of a chip load can lead to excessive tool wear and breakage, while too low of a chip load can lead to rubbing, heat buildup, and inefficient cutting.
Tool manufacturers typically provide recommended chip load values based on the tool type, material, and cutting conditions. You will often find these values in the tool's technical datasheet.
Feed Rate Calculation Examples
Let's look at practical examples for both metric and imperial systems.
Metric Example
A milling cutter with 4 teeth is cutting aluminum. The spindle speed (N) is 2000 RPM, and the feed per tooth (f) is 0.1 mm/tooth.
Calculation:
Result: The feed rate is 800 mm/min.
Imperial (Inches) Example
A milling cutter with 3 teeth is cutting steel. The spindle speed (N) is 1500 RPM, and the feed per tooth (f) is 0.004 inches/tooth.
Calculation:
Result: The feed rate is 18 inches per minute (IPM).
Factors Affecting Milling Feed Rate
Several factors influence the optimal feed rate, and understanding these is vital for effective milling:
- Material type: Softer materials like aluminum allow for higher feed rates because they generate less cutting force and heat. Harder materials such as stainless steel require lower feed rates to manage the increased heat and cutting forces.
- Cutting tool material: Carbide tools are capable of handling higher speeds and feed rates compared to high-speed steel (HSS) tools due to their superior hardness and heat resistance.
- Tool diameter: Larger diameter tools typically require slower feed rates to prevent excessive tool wear and manage the increased cutting forces due to the larger contact area.
- Desired finish: For smoother surface finishes, lower feed rates are recommended. This reduces the size of the cut marks and improves the overall quality of the machined surface.
- Machine rigidity: Less rigid machines require more conservative feed rates to minimize vibration and chatter, which can lead to poor finish and tool damage. A more stable machine allows for faster removal of material.
- Depth of Cut: As the depth of cut increases, the amount of material being removed also increases. This generally requires a reduction in the feed rate to prevent tool overload.
- Radial Engagement: The amount of the cutter engaged with the workpiece (also called width of cut) also influences the optimal feed rate. Higher radial engagements typically require lower feed rates.
- Vibration and Chatter: Vibrations during milling can lead to poor surface finish and premature tool wear. Reduce the feed rate to minimize these issues, or use other techniques to minimize vibration.
Interactive Milling Feed Rate Calculator
To simplify your calculations, our Milling Feed Rate Calculator handles both metric and imperial units. Simply input the required parameters to calculate the correct feed rate instantly.
How to Use the Calculator:
- Select Unit System: Choose either "Metric (mm/min)" or "Imperial (IPM)."
- Input Parameters: Enter the spindle speed (N), number of teeth (T), and feed per tooth (f).
- Example: Let's say you're using a 4-tooth cutter, with a spindle speed of 2200 RPM and 0.07 mm/tooth feed, select "Metric" and enter N = 2200, T = 4, and f = 0.07.
- Click "Calculate": The calculator will then produce the result F = 616 mm/min.
Common FAQs About Milling Feed Rate
What happens if the feed rate is too high?
Excessive feed rates can lead to tool breakage or rapid wear due to increased stress and heat on the cutting edges. A poor surface finish, potentially with visible chatter marks and inaccuracies in the machined part. Increased chance of overloading the machine, leading to premature wear and potential damage.
What if the feed rate is too low?
Too low a feed rate can lead to heat buildup as the tool rubs instead of cuts. This can damage the cutting tool and reduce its lifespan. Increased machining time, leading to reduced efficiency and productivity. Potential for work hardening on the workpiece material.
How do I choose the correct feed per tooth (f)?
Consult the tool manufacturer's technical documentation for recommended chip load based on the material being machined and the type of cutting tool. Use online resources from reputable machining suppliers to get an indication of starting feed per tooth values. Adjust values based on your particular setup and machining experience to ensure the process is both efficient and effective. Start with a conservative value and increase as long as your tool, machine, and material permit, this will help you reduce tool wear and improve finish.
How does depth of cut influence feed rate?
As the depth of cut increases, the amount of material being removed also increases. Generally, as depth of cut increases, you will need to reduce the feed rate to prevent overloading the tool. Adjust feed rate based on the specific cutting situation, and adjust in smaller increments as you fine-tune the process.
What is the relationship between feed per tooth and chip load?
Feed per tooth (f) and chip load are two different names for the same concept. When talking about milling, the feed per tooth is often used. They describe how much material is removed by each tooth of the cutting tool, per rotation.
Example Use Cases
Use Case 1: Aluminum Milling (Metric)
- Tool: 6-teeth carbide cutter
- Spindle speed: 2500 RPM
- Feed per tooth: 0.08 mm/tooth
Feed Rate:
𝐹 = 2500 * 6 * 0.08 = 1200 mm/min
Use Case 2: Steel Milling (Imperial)
- Tool: 4-teeth HSS cutter
- Spindle speed: 1200 RPM
- Feed per tooth: 0.005 inch/tooth
Feed Rate:
𝐹 = 1200 * 4 * 0.005 = 24 IPM
Use Case 3: Stainless Steel Milling (Metric)
- Tool: 3-teeth carbide cutter
- Spindle speed: 800 RPM
- Feed per tooth: 0.04 mm/tooth
Feed Rate:
𝐹 = 800 * 3 * 0.04 = 96 mm/min
Conclusion
Calculating the correct feed rate is crucial for efficient and accurate milling operations, as well as extending the tool's life. Use our Milling Feed Rate Calculator to streamline your work, whether you're dealing with metric or imperial units. By understanding the key factors and formulas, you can optimize your machining process with ease.
Experimentation and adjustment might be required depending on your setup, but understanding the process and using the correct values will always bring you one step closer to an optimized milling process.
Feed Rate Calculator
Calculate optimal feed rates based on cutter geometry and cutting parameters. Switch between metric and imperial units as needed.